Cải thiện hiệu suất nhờ tích hợp cách tiếp cận tự động hóa và Kaizen
Một khung tích hợp thống nhất thể hiện cách tiếp cận Kaizen và tự động hóa được hợp nhất để tái cấu trúc quá trình sản xuất nhằm đạt được cải thiện hiệu suất đáng kể.
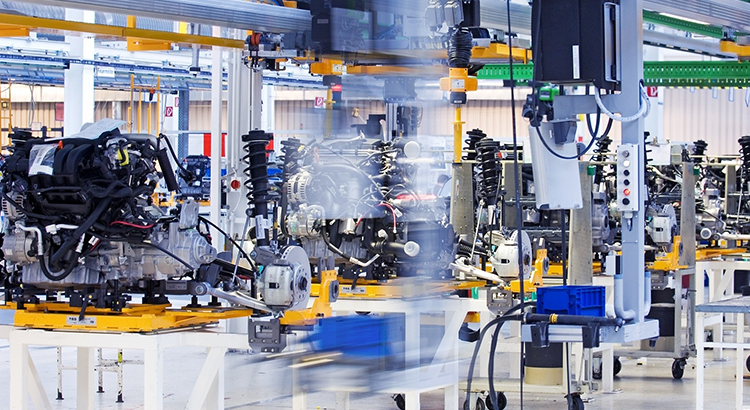
Những khuyến nghị từ cách tiếp cận khác nhau đôi khi gây ra sự nhầm lẫn cho người quản lý về mức độ ưu tiên của các hành động và việc đo lường hiệu quả tiếp theo. Một khung tích hợp thống nhất thể hiện cách tiếp cận Kaizen và tự động hóa được hợp nhất để tái cấu trúc quá trình sản xuất nhằm đạt được cải thiện hiệu suất đáng kể. Khung tích hợp bao gồm tám giai đoạn và chu trình PDCA để cải tiến liên tục.
Thứ nhất, hình dung tương lai của doanh nghiệp. Người quản lý phải sử dụng tư duy sáng tạo để đề xuất một quá trình mới có thể cải thiện hiệu quả sản xuất.
Trong quá trình nghiên cứu, trưởng phòng kỹ thuật nhà máy đã áp dụng công nghệ nhóm để sắp xếp lại xưởng ống và đề xuất cách bố trí xưởng ống “tối ưu” mà không có sự ràng buộc nào. Theo cách bố trí đề xuất này, chiều dài trong mỗi dây chuyền sản xuất ngắn hơn nhiều, thời gian luân chuyển ống nguyên liệu được giảm xuống. Dự thảo bố cục này đã tạo ra sự hứng thú với việc thiết kế lại quá trình sản xuất.
Thứ hai, tổ chức một đội cải tiến và thiết lập mục tiêu. Quá trình là tập hợp các hoạt động hoặc nhiệm vụ sử dụng đầu vào, tăng thêm giá trị và cung cấp đầu ra để hoàn thành một mục tiêu. Hầu hết các dự án tái cấu trúc quá trình sản xuất yêu cầu một nhóm đa chức năng với các thành viên từ các bộ phận khác nhau do tính chất liên quan giữa các bộ phận trong quá trình.
Trong quá trình thực hiện cải tiến, một nhóm bao gồm các trưởng phòng thiết kế và quản lý xưởng ống. Mục tiêu của nhóm là nghiên cứu khả năng tỷ lệ sản xuất tăng 25% và giảm năm công nhân trong xưởng sản xuất ống. Nhóm dự án này sẽ xem xét các đề xuất từ cách tiếp cận khác nhau và quyết định cách thực hiện chương trình cải tiến đạt được mục tiêu.
Thứ ba, kiểm tra quá trình hiện có. Một thực tế phổ biến là bắt đầu thiết kế lại hệ thống bằng cách đánh giá hệ thống hiện có. Đây là tiêu chuẩn cho hệ thống tương lai và là cơ sở quan trọng cho bất kỳ dự án cải tiến nào. Nhóm dự án đã mất khoảng hai tháng để xem xét các quá trình sản xuất hiện có.
Các tài liệu được thiết lập đính kèm trong báo cáo cuối cùng của dự án và sẽ không được mô tả ở đây. Tuy nhiên, sử dụng sơ đồ để lập sơ đồ quá trình rất hữu ích trong việc phân tích quá trình sản xuất. Xác định các cơ hội tái cấu trúc quá trình và khả năng hiện tại. Để xác định các cơ hội tái cấu trúc quá trình, người quản lý phải có hiểu biết sâu hơn về các quá trình từ công nghệ cho phép hoặc từ các kỹ thuật quản lý mới.
Việc nghiên cứu hai cách tiếp cận cho trường hợp của doanh nghiệp dẫn đến một số gợi ý và xác định nhiều thay đổi có thể được đề xuất. Một số trong số thay đổi chỉ đơn giản là những thay đổi nhỏ trong nhà máy hiện có, nhưng một trong những khái niệm từ nhóm cải tiến Kaizen đã dẫn đến việc thiết kế lại quá trình sản xuất một cách toàn diện. Khái niệm này tạo cơ hội cho sự đột phá về hiệu suất, mà nhóm dự án quyết định thực hiện.
Thứ tư, thiết kế quá trình mới. Với đầu vào từ các giai đoạn trước, nhóm dự án có thể thiết kế một quá trình mới. Những người tham gia vào việc tái cấu trúc quá trình nên liên tục đặt câu hỏi về những quá trình hoặc nhiệm vụ nào có thể bị dừng, tái cấu trúc hoặc cải tiến.
Trong trường hợp này, nhóm dự án đã áp dụng ý tưởng “uốn ống sau khi ống được hàn” thay vì khái niệm “hàn ống sau khi ống đã uốn” hiện có trong việc thiết kế lại quá trình sản xuất của xưởng sản xuất ống. Các thành viên trong nhóm đã thảo luận về thiết kế mới từ các khía cạnh khác nhau: quản lý (tác động của nguồn nhân lực), thiết bị (tính khả thi của phần cứng và phần mềm), và cơ sở vật chất (bố trí kèm theo của quá trình sản xuất mới) để điều chỉnh quá trình sản xuất mới. Ví dụ, các kỹ sư từ bộ phận thiết kế đã tính toán tỷ lệ ống có thể phù hợp trong quá trình thiết kế mới, dựa trên bản vẽ của một số tàu hiện có và thuyết phục mọi thành viên trong nhóm rằng cách làm mới là khả thi.
Thứ năm, thực hiện quá trình mới. Giai đoạn này liên quan đến việc thực hiện quá trình mới. Lưu ý rằng quá trình tái cấu trúc cần được điều chỉnh vì các vấn đề xuất hiện trước và sau khi thiết lập. Luôn có sự đánh đổi trong giai đoạn thực hiện với chi phí, công nghệ và các vấn đề khác. Đó là lý do tại sao khung tích hợp được đề xuất có bản chất lặp lại.
Thứ sáu, cải tạo cơ sở hạ tầng. Trong thời gian thực hiện dự án, nhóm dự án nhận thấy rằng phương pháp mô phỏng là công cụ quan trọng để giao tiếp hiệu quả giữa các thành viên trong nhóm và để dự đoán điểm nghẽn có thể xảy ra và hiệu suất kỳ vọng của quá trình mới.
Thứ bảy, đo lường hiệu suất. Cuối cùng là phải xác định mức độ thành công của dự án tái cấu trúc theo mục tiêu đã đặt ra trong giai đoạn trước. Như đã chỉ ra trong nhiều báo cáo, việc cải thiện 50-60% chi phí và năng suất là một mục tiêu thực tế.
Thứ tám, chuẩn hóa quá trình mới. Trước khi bắt đầu một dự án tái cấu trúc quá trình mới, cần phải tiêu chuẩn hóa quá trình mới nếu doanh nghiệp cố gắng duy trì hoạt động tốt như mong đợi. Sự sẵn có của nguồn nhân lực có trình độ, trang thiết bị đầy đủ và các tài liệu liên quan là các yếu tố quan trọng trong việc chuẩn hóa quá trình mới.
Nói chung, giáo dục và đào tạo nhân viên trong bối cảnh quá trình mới là rất quan trọng để duy trì hiệu suất như cũ, nếu không muốn nói là tốt hơn. Vì quá trình mới rất khác biệt so với quá trình ban đầu, nên thực tế lãnh đạo cao nhất có thể cảm thấy rằng việc thực hiện một thay đổi mang tính “cách mạng” như vậy là quá rủi ro.
Trong thời gian thực hiện dự án, các lãnh đạo doanh nghiệp đã do dự về việc thực hiện quá trình mới và các thành viên trong nhóm dự án gặp khó khăn trong việc thống nhất sử dụng phương pháp mô phỏng, mặc dù bố cục mới có thể hợp lý. Mô phỏng được công nhận là kỹ thuật rất hữu ích để thiết kế và đánh giá các cơ sở sản xuất phức tạp. Như phần cứng công nghệ máy tính tiếp tục phát triển và ngày càng có nhiều phần mềm mô phỏng được bán trên thị trường, một số nghiên cứu đã được tiến hành liên quan đến mô phỏng tương tác trực quan của một hệ thống sản xuất trong thập kỷ qua.
Nhìn chung, các nghiên cứu này đã chỉ ra rằng việc đưa hoạt ảnh vào làm công cụ mô phỏng có thể nâng cao khả năng trình bày với người dùng và cải thiện giao tiếp giữa người quản lý và người lập trình hệ thống. Với việc bổ sung khả năng điều khiển tương tác, người dùng có thể tạm dừng thử nghiệm mô phỏng bất kỳ lúc nào để xem thống kê và/hoặc thay đổi một số thông số; Quá trình phát triển phương pháp mô phỏng tương tác trực quan, kèm theo các thực hành trong dự án, được trình bày như sau:
Xác định mục tiêu: Mô hình mô phỏng tốt là mô hình chỉ bao gồm hệ thống quan tâm và có thể cung cấp câu trả lời cho các nhà quản lý. Cần phải có định nghĩa chính xác về mục tiêu. Mối quan tâm chính của dự án này là tốc độ sản xuất ước tính và số lượng công nhân cần thiết trên sàn nhà xưởng cho cả quá trình sản xuất hiện tại và mới. Thời gian để hoàn thành các thí nghiệm mô phỏng cũng phải ngắn nhất có thể.
Thu thập và nhập liệu: Dữ liệu đầy đủ và chính xác phải có sẵn để xây dựng mô hình mô phỏng và thực hiện các thí nghiệm máy tính sau đó. Thông tin như nhu cầu, tệp định tuyến của các bộ phận, thời gian xử lý của các bộ phận, thời gian di chuyển từ vị trí này đến vị trí khác thường được yêu cầu.
Các nghiên cứu về thời gian và chuyển động truyền thống và phân tích thống kê đã được thực hiện trong dự án này để tìm kiếm thông tin cần thiết. Dữ liệu hiệu suất từ các cơ sở mới được thu thập từ các nhà cung cấp.
Vẽ bố cục và sơ đồ quá trình: Đối với mô hình mô phỏng động, cần vẽ bố cục cho phông nền trong quá trình thực hiện mô hình mô phỏng. Trong quá trình dự án, kích thước của xưởng sản xuất ống và vị trí của từng máy đã được đo. Các sơ đồ cho quá trình mới và quá trình sản xuất ống hiện có đã được vẽ. Một sơ đồ quá trình bộ phận cũng là một đầu vào cần thiết của phần mềm để hiển thị cách các bộ phận chuyển động trong quá trình sản xuất trong nhà máy.
Kiểm tra và xác nhận: Mô hình mô phỏng máy tính cần được xác minh xem nó có hoạt động như dự kiến và phản ánh hoạt động của hệ thống thực hay không. Một mô hình mô phỏng dễ dàng hơn để xác minh và xác nhận vì người dùng có thể theo dõi kết quả của từng hoạt động trên màn hình. Đầu ra được tạo ra từ mô hình mô phỏng, dựa trên quá trình hiện có, cung cấp một điểm chuẩn để so sánh “thực tế” của nó.
Kết quả và phân tích: Đầu ra, chẳng hạn như tốc độ sản xuất trung bình hoặc việc sử dụng mỗi trung tâm làm việc, có thể dễ dàng được tìm thấy và thu thập bằng các gói mô phỏng. Người dùng cũng có thể thử nghiệm các bố cục thay thế để cải thiện hiệu suất của hệ thống.
Nhóm dự án đã sử dụng mô phỏng như một kênh giao tiếp để xem xét các kết quả có thể có của việc sử dụng các thông số vận hành khác nhau trong xưởng việc làm. Promodel PC phiên bản 5.0 được chọn làm gói phần mềm mô phỏng. Gói này cung cấp giao diện đầu vào / đầu ra dễ dàng, khả năng trình bày đồ họa động và các công cụ phân tích khác nhau với giá cả phải chăng.
Các mô hình mô phỏng được xây dựng và thực hiện trên một PC tương thích với IBM. Việc phát triển một mô hình mô phỏng cho dự án, bao gồm gỡ lỗi, mất chưa đầy hai tuần; tuy nhiên, phải mất hơn ba tháng để thu thập và xác minh các dữ liệu đầu vào cần thiết.
QTC-PKH
Bình luận